Measures and ways to prevent stomatal defects:
1. Ensure the refining and degassing quality of aluminum alloy smelting, the surface of the alloy ingot and the tools are dry, and the returned material is clean. Select good refining agent and degassing agent, control the smelting temperature, avoid overheating, reduce the gas content in the molten aluminum, and carry out degassing treatment. Remove oxides such as liquid surface scum and foam in time to prevent the gas from being brought into the die casting again.
2. Select a good release agent and spraying process. The selected release agent should not generate gas in die casting and have good release performance.
3. Ensure that the mold exhaust groove and overflow groove are in the correct positions, and the sequential filling is conducive to the discharge of the cavity gas, the exhaust is smooth and not blocked, and the exhaust is smooth to ensure that the gas in the mold is completely discharged, especially at the final polymerization of the aluminum liquid. The exhaust passage must be unobstructed. The sprue and runner have sufficient length (>50mm) to facilitate the smooth flow of the alloy liquid and the opportunity for gas discharge. The gate thickness and gate direction can be changed, and overflow grooves and exhaust grooves can be provided at the position where the air holes are formed. The sum of the cross-sectional area of the overflow products cannot be less than 60% of the sum of the cross-sectional area of the inner gate, otherwise the slag discharge effect will be poor.
4. Select the coating with good performance and control the spray amount.
5. Adjust the parameters of the die casting, especially the injection speed, control the casting temperature, and the filling speed should not be too fast to achieve an orderly and stable flow state, and prevent separation and eddy current from forming entrained air.
6. In product design and mold design, attention should be paid to the use of core pulling and cooling to minimize wall thickness differences.
7. For the pores that often appear in the fixed parts, it should be improved from the mold and design, whether there is a sharp corner area or a dead area, whether there is a change in the cross-sectional area of the gating system, and use the computer to simulate the filling process and judge to select reasonable process parameters.
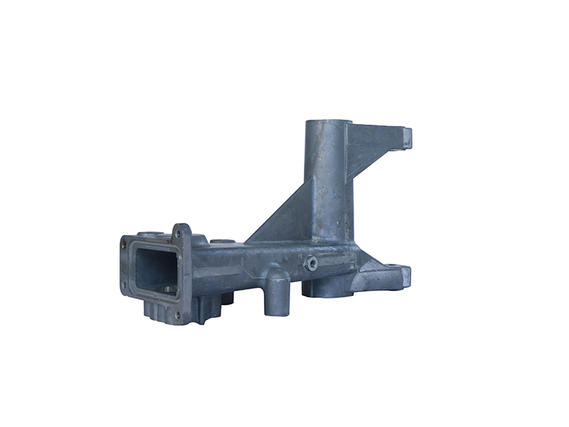
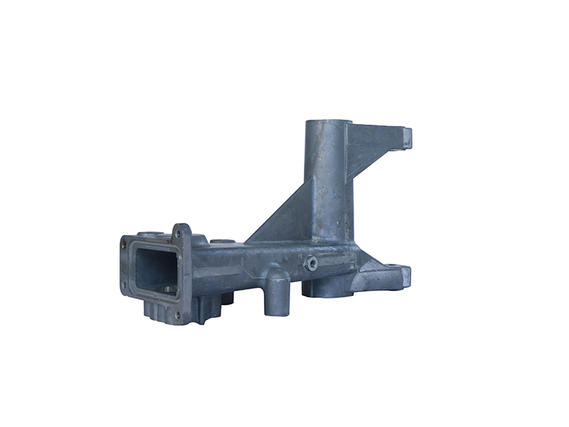