The quality of die-casting parts is related to the selection of raw materials. The prerequisite for die-casting high-quality die-casting parts is to choose high-quality raw materials.
1. Silicon (Si) - Die Casting Aluminum Alloy Element
Silicon is the main element of most die cast aluminum alloys. It can improve the casting performance of the alloy. The general content is 9.6%-12%. When the silicon content exceeds 12%, silicon and aluminum form a hypereutectic, and when there are too many impurities such as copper and iron, hard spots of free silicon appear. , making the cutting process difficult, and the high silicon aluminum alloy has a serious erosion effect on the casting crucible. Silicon and aluminum can form a solid solution. At 577°C, the solubility of silicon in aluminum is 1.65%, at room temperature it is 0.2%, and when the silicon content reaches 11.7%, silicon and aluminum form a eutectic. Improve the high temperature fluidity of the alloy, improve the wear resistance, reduce the tendency of hot cracking and shrinkage. Binary aluminum-based alloys have high corrosion resistance. When the content of silicon in the alloy exceeds the eutectic composition, and there are too many impurities such as copper and iron, the hard spots of free silicon appear, which makes cutting difficult, and the high-silicon aluminum alloy will erode the casting crucible.
Serious effect.
2. Copper (Cu)--a die-casting aluminum alloy element
Copper and aluminum form a solid solution. When the temperature is 548 °C, the solubility of copper in aluminum should be 5.65%, and it will drop to about 0.1% at room temperature. The copper content in the alloy is usually 1.5% ~ 3.5%. Improve the fluidity, tensile strength and hardness of the alloy, but reduce the corrosion resistance and plasticity, and increase the tendency of hot cracking.
3. Magnesium (Mg)--a die-casting aluminum alloy element
Adding a small amount (about 0.2-0.3%) of magnesium to the high-silicon aluminum alloy can improve the strength and yield limit, and improve the machinability of the alloy. The aluminum alloy containing 8% magnesium has excellent corrosion resistance. When the magnesium content is too high, the casting performance becomes poor, the strength and plasticity at high temperature are low, and the shrinkage is large when cooling, so it is easy to produce hot cracks and form looseness.
4. Zinc (Zn)--a die-casting aluminum alloy element
Zinc can improve fluidity, improve casting performance, and improve tensile strength in aluminum alloys, but the tendency of hot cracking increases and corrosion resistance decreases, generally less than 1.2%. As for the ZL401 aluminum alloy with high zinc content, it has good casting properties and mechanical properties, and the cutting process is also relatively good.
5. Iron (Fe)--a die-casting aluminum alloy element
Hazardous impurities are present in all aluminum alloys. When the iron content in the aluminum alloy is too high, iron exists in the alloy in the form of flake or needle-like structures of FeAl3, Fe2Al7 and Al-Si-Fe, which reduces the mechanical properties. This structure will also reduce the fluidity of the alloy. The hot cracking property increases, but the adhesion of aluminum alloy to the mold is very strong, especially when the iron content is below 0.6%. When it exceeds 0.6%, the sticking phenomenon will be greatly reduced, so the iron content should generally be controlled within the range of 0.6 to 1%, which is beneficial to die casting, but the maximum cannot exceed 1.5%.
6. Manganese (Mn)--a die-casting aluminum alloy element
Manganese can reduce the harmful effects of iron in aluminum alloys, and can make the flake or needle-like structure formed by iron in aluminum alloys into fine crystal structures, so generally aluminum alloys are allowed to contain less than 0.5% of manganese. When the manganese content is too high, it will cause segregation.
7. Nickel (Ni) - Die Casting Aluminum Alloy Element
Nickel in aluminum alloy can improve the strength and hardness of the alloy and reduce the corrosion resistance. Nickel has the same effect as iron, which can reduce the erosion of the alloy on the mold, and at the same time it can neutralize the harmful effect of iron and improve the welding performance of the alloy. When the nickel content is 1-1.5%, the casting can get a smooth surface after polishing. Due to the lack of nickel sources, nickel-containing aluminum alloys should be used as little as possible.
8. Titanium (Ti)--a die-casting aluminum alloy element
The addition of a trace amount of titanium to the aluminum alloy can significantly refine the grain structure of the aluminum alloy, improve the mechanical properties of the alloy, and reduce the hot cracking tendency of the alloy.
9. Strontium - die-casting aluminum alloy element
Strontium is a surface active element, crystallographically, strontium can change the intermetallic
Compound Phase Behavior. Therefore, modification treatment with strontium element can improve the plastic workability of the alloy and the quality of the final product. Due to the advantages of strontium's long-term modification effect, good effect and reproducibility, etc., the use of sodium has been replaced in Al-Si casting alloys in recent years. Add 0.015%~0.03% strontium to the aluminum alloy for extrusion, so that the β-AlFeSi phase in the ingot becomes a Chinese character-shaped α-AlFeSi phase, which reduces the ingot homogenization time by 60%~70%, and improves the mechanical properties of the material. Plastic workability; improve product surface roughness. For high silicon (10%~13%) deformed aluminum alloys, adding 0.02%~0.07% strontium element can reduce the primary crystal to a minimum, and the mechanical properties are also significantly improved, and the tensile strength бb is increased from 233MPa to 236MPa
, the yield strength б0.2 increased from 204MPa to 210MPa, and the elongation б5 increased from 9% to 12%. The addition of strontium to the hypereutectic Al-Si alloy can reduce the size of the primary crystal silicon particles, improve the plastic workability, and enable smooth hot rolling and cold rolling.
10. Zirconium - die-casting aluminum alloy element
Zirconium is also a common additive for aluminum alloys. Generally, the amount added to the aluminum alloy is 0.1%~0.3%. Zirconium and aluminum form ZrAl3 compounds, which can hinder the regeneration of aluminum alloys.
The crystallization process refines the recrystallized grains. Zirconium can also refine the casting structure, but the effect is smaller than that of titanium. In the presence of zirconium, titanium and boron refinement is reduced
grain effect. In Al-Zn-Mg-Cu alloys, since the influence of zirconium on quenching sensitivity is smaller than that of chromium and manganese, zirconium should be used instead.
Chromium and manganese refine the recrystallized structure.
11. Chromium - die-casting aluminum alloy element
Chromium is a common additive element in Al-Mg-Si-based, Al-Mg-Zn-based, and Al-Mg-based alloys. At 600 °C, the solubility of chromium in aluminum is 0.8%, and it is basically insoluble at room temperature. Chromium forms (CrFe)Al7 and (
CrMn)Al12 and other intermetallic compounds hinder the nucleation and growth process of recrystallization, have a certain strengthening effect on the alloy, and can also improve the toughness of the alloy and reduce the susceptibility to stress corrosion cracking. But the venue increases the quenching sensitivity, making the anodic oxide film yellow. The addition of chromium in aluminum alloys generally does not exceed 0.35%, and decreases with the increase of transition elements in the alloy.
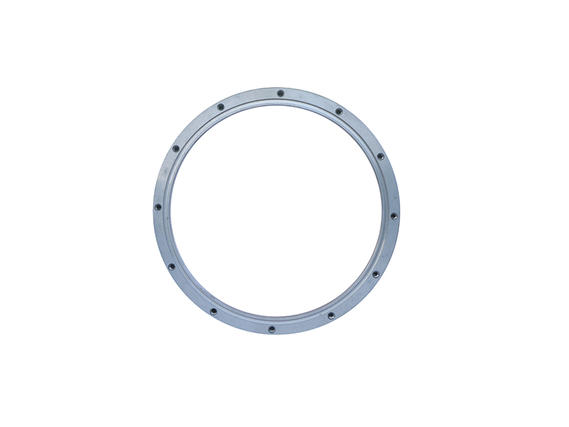
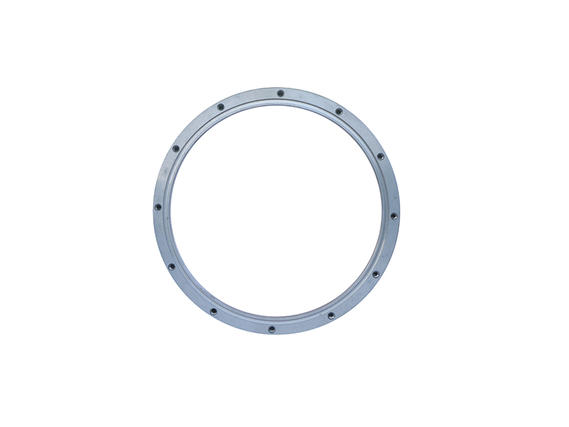