Talking about the advantages and disadvantages of die casting process
advantage:
(1) Metal parts with complex shapes, clear outlines, thin walls and deep cavities can be manufactured. Because molten metal maintains high fluidity at high pressure and high speed, metal parts that are difficult to machine by other processes can be obtained.
(2) The dimensional accuracy of die castings is high, up to IT11-13 grade, sometimes up to IT9 grade, the surface roughness is Ra0.8-3.2um, and the interchangeability is good.
(3) The material utilization rate is high. Due to the high precision of die-casting parts, they can be assembled and used only after a small amount of machining, and some die-casting parts can be directly assembled and used. Its material utilization rate is about 60%--80%, and the blank utilization rate is 90%.
(4) High production efficiency. Due to high-speed filling, the filling time is short, the metal industry solidifies rapidly, and the die-casting operation cycle speed is fast. Among various casting processes, the die casting method has the highest productivity and is suitable for mass production.
(5) It is convenient to use inlays. It is easy to set the positioning mechanism on the die-casting mold, which is convenient for inserting the inlay and meeting the special performance requirements of the die-casting part.
shortcoming:
1. Due to high-speed filling and rapid cooling, the gas in the cavity cannot be discharged in time, resulting in the existence of pores and oxide inclusions in die castings, thereby reducing the quality of die castings. Due to the expansion of the gas in the pores at high temperature, the surface of the die casting will bubble, so the die casting with pores cannot be heat treated.
2. Die-casting machines and die-casting molds are expensive and not suitable for small batch production.
3. The size of die castings is limited. Due to the limitation of the clamping force of the die-casting machine and the size of the die, it is impossible to die-cast large-scale die-casting parts.
4. The types of die-casting alloys are limited. Since the die-casting mold is limited by the operating temperature, it is currently mainly used for die-casting zinc alloy, aluminum alloy, magnesium alloy and copper alloy.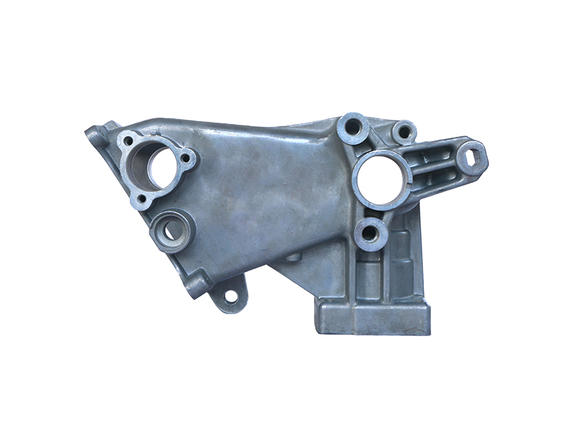
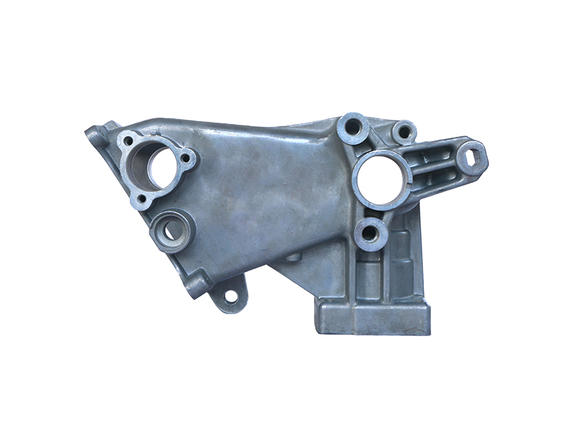